企業の開発部門のお手伝いをさせて頂くことも多く、小ロット・多品種・短納期の対応、価格的にもメリットがある事が要因だと感じております。更に、カーボンの加工のノウハウが多いため、「VA提案」「VE提案」も出来きる事が最大の力であると自負しております。
現在、各素材メーカー様より新しい材料が開発される一方、カーボンの使用環境は益々厳しくなっており、より複雑な加工、より優れた耐性、より多機能な材料が求められております。
そんな中、弊社の強みとなっている
- 各素材メーカー様の材料から使用条件にあう材料の選定が出来ること
- 長年の蓄積された経験からVA提案・VE提案力が優れていること
- 常に最先端の加工のお手伝いをさせて頂き情報が豊富なこと
- 小ロット・多品種・短納期の対応に柔軟で競争力があること
- 少人数精鋭部隊で会社を運営し情報が守られること
※VA提案(=Value Analysis)材質や形状を変更してコストダウン・機能アップをねらう事
※VE提案(=Value Engineering)コストを上げずに機能を向上させる提案のこと
ダイヤ焼結用、カーボン型
30〜40年程前、ダイヤ焼結型は、カーボン型にパンチを一方向から押し出す分解出来ないカーボン型でした(下記、左図)。
焼結されたダイヤチップを取り外す際、カーボンのパンチを叩き込むと、焼結ダイヤがカーボン型に擦れ傷が入ってしまう事があります。型に傷が付くと、次のダイヤチップ焼結の際に型の傷跡がチップに付いてしまい、型としての機能を果たせなくなってしまう為、カーボン型の交換頻度が高くなります。
そこで、弊社では、カーボンの型を分割することにより(下記、右図)、焼結後のパンチの取り出しが容易で型に傷が付くこともなく、取り外すことが出来る分割式のカーボン型を提案いたしました。
とりわけ、弊社のカーボン型は嵌合精度がとてもよく、作業性・製品の仕上がりがとてもいいことご好評頂いております。
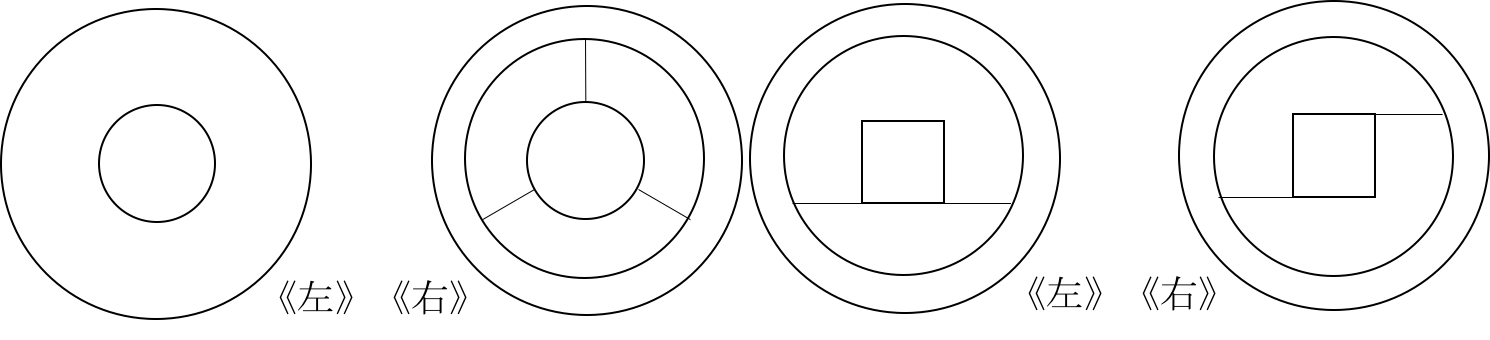
工業炉用、炭素繊維リボンヒーター
熱処理炉などの工業炉には、セラミックやカーボンの様々な材料から作られている部品が組み合わさり出来ています。
使用されている部品の一つに、炭素繊維の織物をリボンヒーターとして使われている工業炉があります。
近年では、炭素繊維リボンヒーターを使った熱処理炉は少なくなっているのですが、数十年頑張って働いている工業炉もまだまだあります。
しかしながら、工業炉メーカー様も余りにも古くなった炉に対しては部品の調達が難しくなり、アフターメンテナンスが出来なくなる事もあります。その一つが炭素繊維のリボンヒーターでした。
弊社では、長年、熱処理をされている会社様とお取引をさせて頂いており、炭素繊維リボンヒーターを製造するメーカーがなくお困りのお客様がいらっしゃいました。
そこで、熱処理をされていらっしゃるお得意先様や、炭素繊維の加工をされている仕入先メーカー様のご協力を頂き、様々な試行錯誤を繰り返し、約2年の歳月をかけて、炭素繊維のリボンヒーターを製品化した実績がございます。
現在では、提供しておりました炭素繊維の原糸の仕入れが出来なくなった事と、電子制御がされていない昔ながらの織機がなくなってしまった為、提供できなくなっております。
ガラス瓶製造装置用、口元チャック
現在、ガラス加工にカーボンが使用されるのは一般的な事ですが、60〜70年前までは、分割式のガラス成形型は樫の木で作られておりました。また、ガラスの持ち運びや、下敷きに使われているカーボンクロスは、新聞紙に水を含ませたものを使っておりました。その為、ガラス加工は機械化が難しく、一日の生産本数も少なく、ガラス瓶の価格も非常に高価でした。
その後、ガラスの量産化に伴い、金属製金型を使用して製ビンを行うようになりましたが、ガラスの金型の溶着を防ぐ為に大量の離型材を毎回塗布して生産していました。そこでガラスに濡れない特性を持ち、かつ、耐熱性が高いカーボンを製ビンの成型治具に使えないかと検討・研究が行われました。
しかし、ガラス瓶の成型に使われているガラスの口を掴むチャック(口型)の製瓶金型は、当時の加工機械では形状が難しく、対応出来る会社が少なく、また、ガラスの合わせ型は嵌合がしっかりしていても繋ぎ目がどうしてもガラスに転写するため、材料の選定も非常に困難を極めました。
そこで弊社は、水分を吸収・透過する材料を入手しました。大量の水を含ませる事が出来るため、溶解ガラスの熱で型の内部に水蒸気膜を作り、ガラスに筋が入りにくい状況を作る事が出来、繋ぎ目の形状の問題を解決しました。
現在では、ガラス瓶の生産には、C/Cコンポジットが多く使用されております。
メカニカルシール用、樹脂含浸材料
東日本大震災の時は、全国的に電車の間引き運転が必要だとか、工場の生産がストップし製品が作れないや、工場の装置や設備が動かせないといわれた時期でした。
それは、電車にはカーボンブラシ、装置や製品にはカーボン軸受けなどの、メカニカルシール部品が使用されており、震災の影響で、大手製造メーカー様の生産が、ストップしてしまった事が理由でした。
その一つに、樹脂含浸を施したメカニカルシールがありました。
一部のカーボン製品には、シール性や耐磨耗性などを向上させる為に、材料に含浸処理を行います。
震災当時、材料確保が難しい中、弊社では、一時的な対応策として提供した樹脂含浸材料があります。
物性表なども準備できない状況で、お客様に御使用して頂きました。
実際にお使いいただくと「優れた材料で、継続して使いたい」とおっしゃって頂いたアイテムもございます。
エンドユーザー様ならびに、弊社と一緒になってご尽力頂きました協力会社様の手助けもあり、現在も継続して提案している材料となります。
数十年前までは、弊社には含浸処理設備が有り、樹脂含浸材料の加工は、その頃から行っております。
カーボン軸受けの加工では、特にスパイラル加工の形状が安定しており、優れた軸受けを提供しております。